Troubleshooting TwinCAT 3 Safety Errors: Solutions for Common Issues with FSoE, EDM, Alias Devices, and Module Descriptions
1.1. Could you please clarify if the error that occurs after the safety program download ("SDO Abort, Data cannot be transferred or stored to the application because of local control") will have any impact?
The error message shown suggests that the safety logic has not been successfully downloaded.
1.2. How to shut down AX5805 using the SLS method
In TwinCAT 3 software, the AX5805 is automatically recognized during IO scanning, but it does not include the SLS function.
After importing alias devices in the safety logic, you need to add SLS manually.
You can refer to the AX8000 manual for a usage example of SLS safety logic:
AX8000 SafeMotionWizard Tutorial
AX5805 has limitations on using older motor encoders. To check supported motor models, refer to:
AX5805 Default Motor Values
1.3. Impact of enabling "testing of outputs active" and "current measurement active" on safety levels
From the following three images, it can be observed that the "el2904 Test pulses" do not affect safety levels, but the output load circuit will affect whether the current monitoring function can be enabled.
1.4. TwinCAT 3 Safety Error: "Multiple templates exist for the AliasDevice. To prevent errors, the loading of safety projects is prohibited. Please fix the following errors and restart TwinCAT."
Error screenshot:
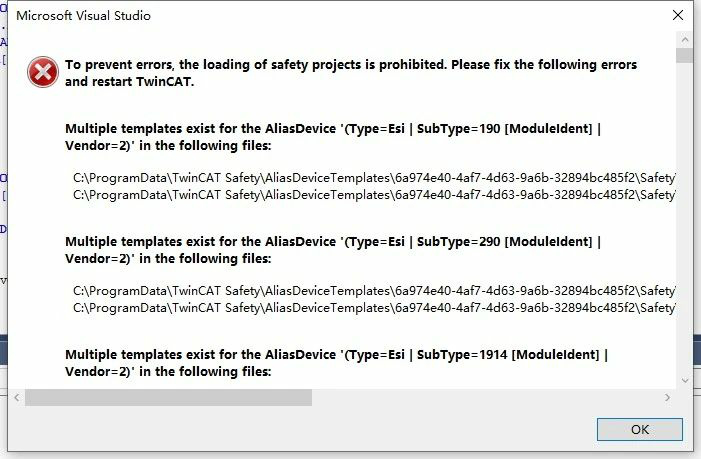
Error Cause:
This is caused by the creation of duplicate Alias devices in the TwinSAFE project, leading to a conflict.
Solution:
Go to the error path C:\ProgramData\TwinCAT Safety\AliasDeviceTemplates\6a974e40-4af7-4d63-9a6b-32894bc485f2\Safety\EtherCAT\Beckhoff Automation GmbH & Co. KG
, find the duplicate files, and keep only one. Then, reactivate the configuration.

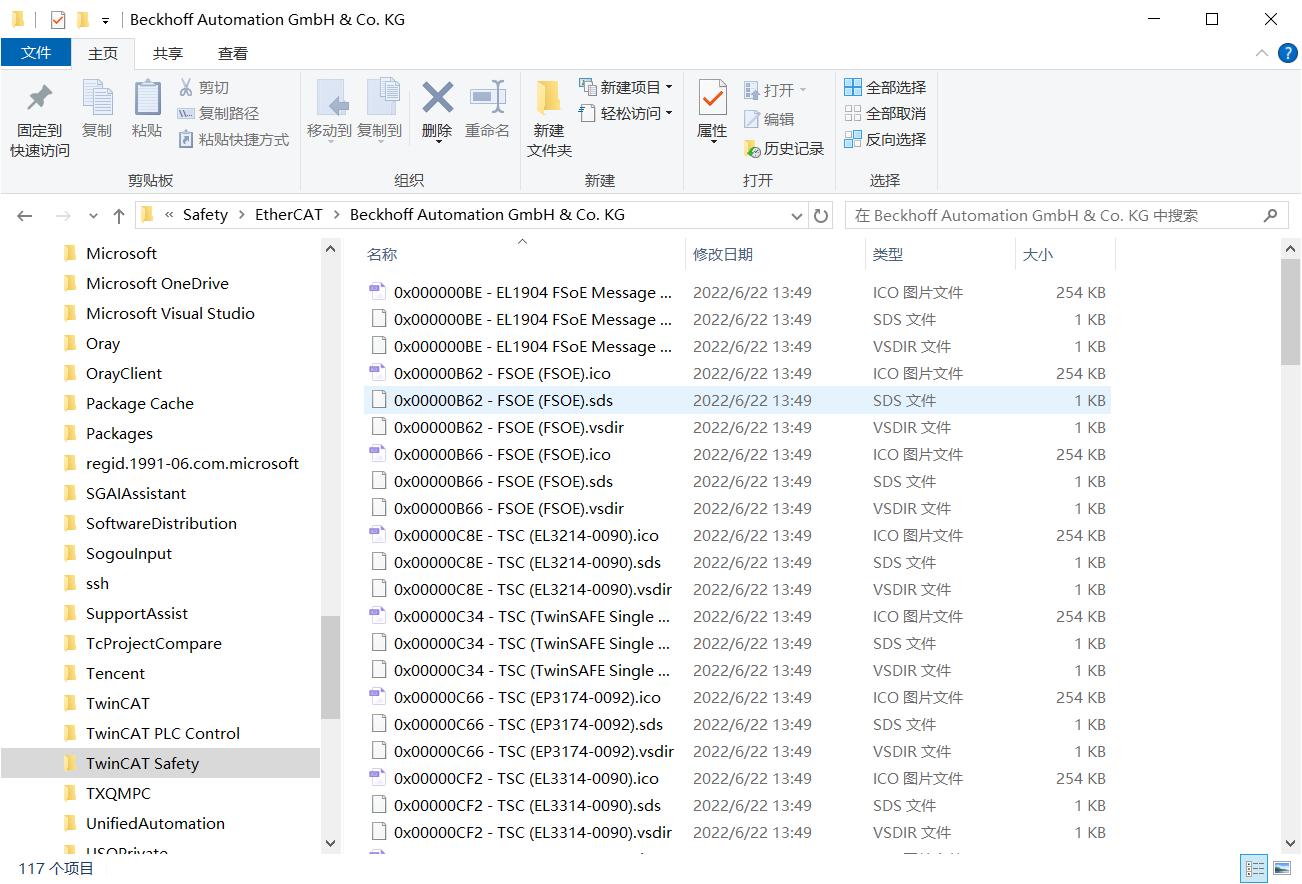
1.5. TwinCAT 3 Safety Error:
"On the 8th connection in state PARAMETER, an FSOE-Reset with Error-Code 6 was received, which means that the communication partner has received an invalid FSOE address."
Error screenshot:
Solution for TwinCAT 3 Safety Error:
This error is typically caused by a 1904 channel issue, which leads to a 1904 module error. However, with the default configuration, the safety program can still run normally.
The communication error occurs because the option "Module Fault is COM ERR" was selected, turning the issue into a communication error, which then triggers the safety error in the safety project.
1.6. Monitoring Current Fault Information in Safety Logic and Modules:
To monitor current fault information, you need to add the Safety Project Online View in the View tab.
In the lower section, a fault information bar will appear. Double-clicking on this information will show detailed fault information.
1.7. Error with Multiple Safety Function Block Pin Links:
Error:
"Andin2 of FBAnd1 is activated but not connected."
Error Cause:
In the image, the part of the safety function block that was previously linked is still showing a black line under the pin, indicating that the pin is still in an active state, even though the link was deleted. This causes the error.
Solution:
Right-click on the black line under the pin and select Change InPort Settings.
Select Deactivated, click1 OK。
After this, the black line will disappear under the pin, and the error will no longer occur.
1.8. EDM: Reliability of Safety Outputs
For the reliability of safety outputs, a closed-loop feedback is needed. This is usually implemented by safety relays or other safety hardware products.
For example, a safety relay has 3 normally open (NO) contacts and 1 normally closed (NC) contact. To prevent contact sticking after long-term use, a fault detection mechanism is necessary. There is a metal hard connection between the 3 NO contacts and 1 NC contact (as shown in Figure 2). If the NO contact becomes NC after the safety output, the NC contact must become NO. If contact sticking occurs, the NC point will not switch to NO.
The EDM signal type in mapping settings can be either safety input or regular input. The EDM in the safety function block handles this hardware situation. When safe-out = 0, EDM's input is 1. When safe-out = 1, EDM's input is 0. If both signals match (either both 1 or both 0), the EDM error will be triggered.
1.9. Inquiry about Safe Over EtherCAT (FSoE)
Question:
Regarding Safe Over EtherCAT (FSoE) as shown in the system diagram, there are regular EtherCAT and FSoE loops. Does the EtherCAT SAFE master rely on the EtherCAT master?
Answer:
Yes, the communication between the two is interdependent.
If the EtherCAT master fails, the FSoE loop will no longer communicate.
Question:
Is it possible to separate the safety loop from the EtherCAT master?
Answer:
No, it cannot be done separately.
However, we recommend using the EK1960. If you only use the safety inputs and outputs of the EK1960, it can function independently of the controller.
1.10. crc32 in module description of fsoe-slave from vendor
Need to Update Safety Module Description File
1.11. Error when Opening Project: "AliasDeviceType not supported"
When opening the project, you encounter the error: "AliasDeviceType not supported." Other colleagues can open the same project without issues, but you receive the error message as shown in the screenshot. After confirming that the TwinCAT 3 and TwinSAFE versions are identical to those of your colleagues, the problem was solved by updating the EtherCAT description file.
Cause:
The issue likely arises because some of the safety modules in the project are newer, and TwinCAT is unable to recognize the new modules, leading to the error message above.